▸ Our Employees
Our Employees
Rosenbauer seeks employees who make a difference with their diversity and ideas. To this end, the company provides an environment in which every employee can contribute their talent and efforts. As an employer, Rosenbauer promotes the health of the workforce and highly prioritizes workplace safety.
Current social and technical developments are changing the environment in which Rosenbauer and firefighting technology operate. As a result, employees’ needs and requirements are changing as well. They count as one of the most vital stakeholder groups for Rosenbauer.
One of HR management’s most important duties is to create a corporate culture and work environment in which employees can evolve and gladly contribute to our mutual success.
EMPLOYEE SATISFACTION AND WORK-LIFE BALANCE
Employee satisfaction encompasses many issues that intersect and interact. Various benefits contribute to Rosenbauer’s image as an attractive employer. In order to maintain employee enthusiasm over the long term, Rosenbauer has developed measures that meet its requirements as an employer on the one hand, and take account of employees’ needs on the other.
Employee recruitment and retention
The overriding aim of the recruitment strategy is to secure a workforce of qualified specialist workers and executives in the long term. The company strives to recruit employees who are still in school or university by offering internships, providing topics for scientific degree theses and presenting the company at career fairs. Technical staff are of key importance in recruitment. The turnover rate of 12.7% underscores Rosenbauer’s image as an attractive employer. At one location in the USA, numerous employees received a new employment contract in 2019, so the turnover there increased more sharply as a result of the remeasurement. Of the people who left the company, 6.7% went into retirement, at an average age of 63.5.
Employee benefits and work-life balance
As an attractive employer, Rosenbauer aspires to offer its employees an optimal work-life balance. Across the Group, 4.8% of employees work part-time, more of them in white-collar than blue-collar jobs. Rosenbauer supports flexible working hours and offers both part-time and flextime work, or work-from-home days.
In Europe, a dedicated family program allows men to also take parental leave. In Leonding alone, 28 men took this opportunity. This figure was 35 at the German locations. To facilitate the return to work for individuals, Rosenbauer runs its own daycare center in Leonding in cooperation with the companies Silhouette and PEZ/Haas, which guarantees parents a regular daycare spot for their children.
Employees are permitted to bring their dogs to work at one location operated by Rosenbauer Brandschutz Deutschland. The employees there confirm that the effect on the working environment is very positive.
Status Goal Proportion of Women
Employment structure
As an employer of global reach, Rosenbauer has 3,828 employees. They are broken down into two categories: Blue-collar workers mainly work in the areas of production, assembly and repair, while salaried employees work in administration, development and sales. Collective labor agreements are held by 58.1% of employees. Apprentices account for 4.1% of all employees; in countries with statutory training and education for apprentices, this figure rises to 6.9%.
White-collar workers | All employees | Blue-collar workers | White-collar workers | ||||||
---|---|---|---|---|---|---|---|---|---|
2019 | 2018 | 2017 | 2019 | 2018 | 2017 | 2019 | 2018 | 2017 | |
Austria | 1,558 | 1,442 | 1,345 | 891 | 823 | 752 | 667 | 619 | 593 |
Germany | 963 | 906 | 853 | 626 | 585 | 551 | 337 | 321 | 302 |
Rest of Europe | 302 | 256 | 240 | 164 | 143 | 121 | 138 | 113 | 119 |
USA | 829 | 841 | 830 | 597 | 600 | 600 | 232 | 241 | 230 |
Rest of World | 176 | 166 | 131 | 116 | 102 | 60 | 60 | 64 | 71 |
Employees of Rosenbauer Group by gender (per 12/31/2019 in % and headcount) | 2019 | 2018 | 2017 |
---|---|---|---|
All employees | |||
Women | 473 | 432 | 416 |
Women in % | 12.4 % | 11.9 % | 12.2 % |
Men | 3,355 | 3,179 | 2,983 |
Men in % | 87.6 % | 88.1 % | 87.8 % |
DIVERSITY AND EQUAL OPPORTUNITIES
Rosenbauer believes that a respectful and open corporate culture promotes and advances diversity. It is therefore committed to a work environment that is free from prejudice and discrimination of any kind. Employees are treated with the same respect and tolerance regardless of their gender, age, sexual orientation and identity, nationality, ethnic origin, religion and ideology. In order to make this absolutely clear to the wider world as well, the company signed the “Diversity Charter” in 2017, which provides a platform for dialog and promoting diversity in the company.
Promotion of equal opportunities
In the recruitment process, care is taken to treat male and female applicants equally. The total percentage of women in the Group is 12.4% and has therefore increased slightly year-on-year.
The share of female executives decreased slightly from 13.2% to 12.1% in 2019. These statistics are based on the most senior level of management at the individual locations. As a manufacturer that takes on apprentices, Rosenbauer’s stated objective is to encourage girls to follow a technical career path. The percentage of young women doing an apprenticeship was 22.6% in 2019. Female apprentices in Production made up 8.9%, representing an increase of nearly 4% compared with 2018 and making a significant contribution to the target of greater diversity.
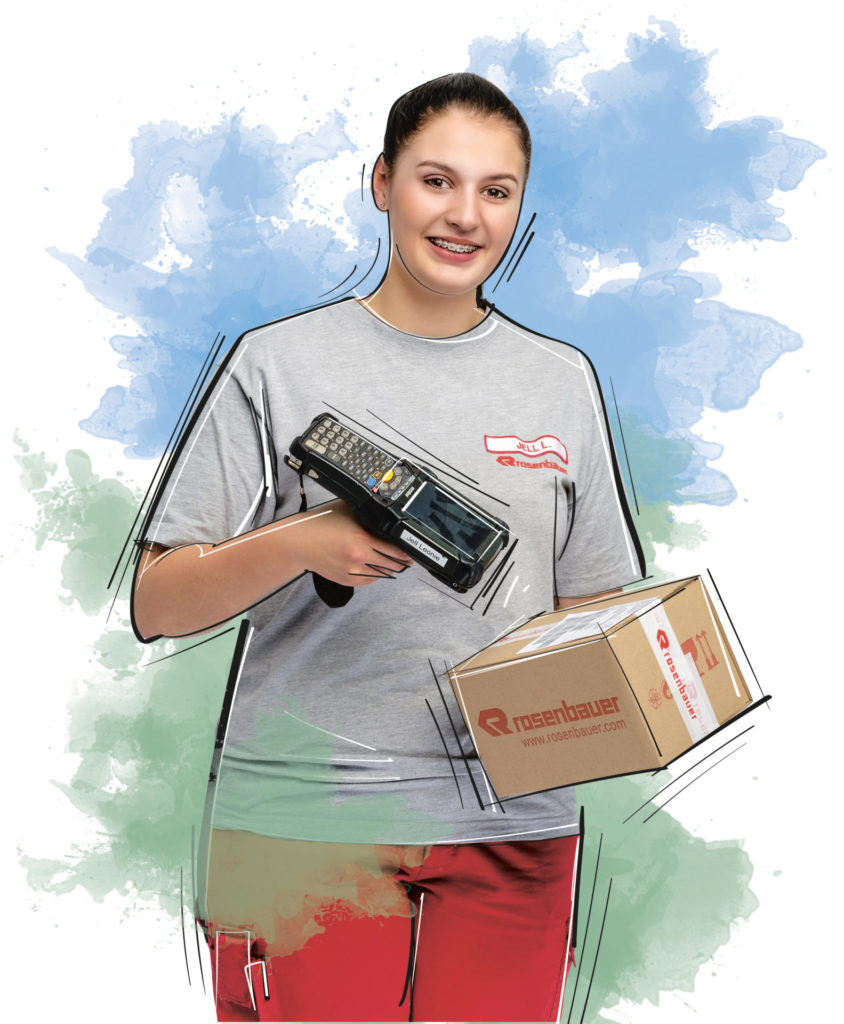
enrich
“Some people are just looking for a job. I am looking for a challenge at work.”
LEONIE JELL
APPRENTICE IN PURCHASE & LOGISTICS
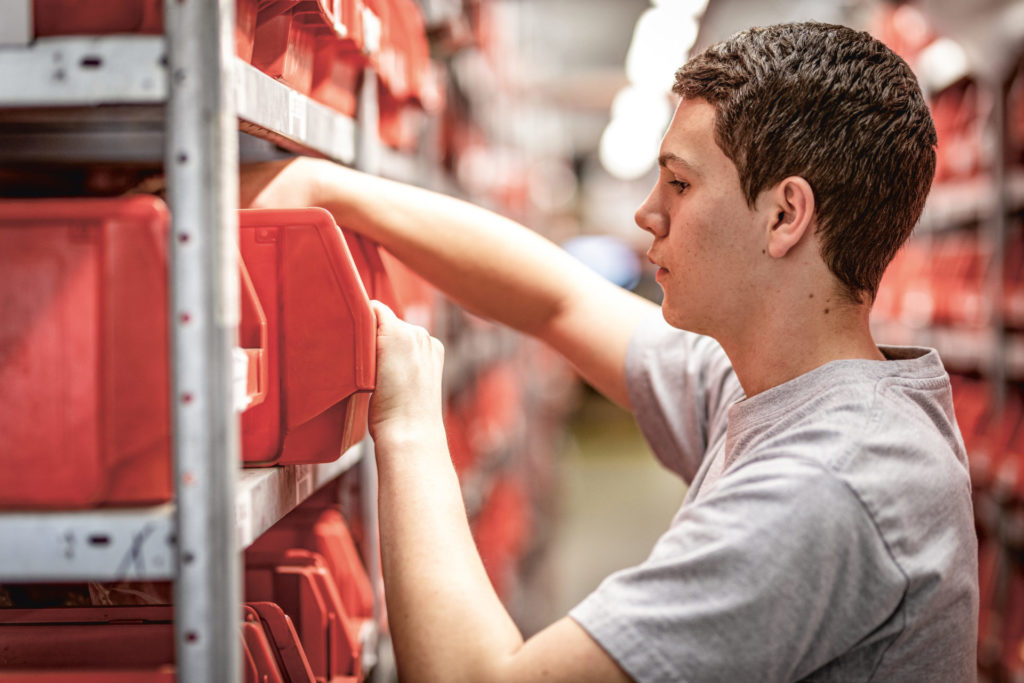
DIVERSITY INSPIRES
We are convinced that an open corporate culture inspires us and makes us successful. This is why we promote diversity and offer our employees various opportunities to unlock their potential: from training and continuing professional development to educational leave and participation in competitions.
TRAINING AND CONTINUING PROFESSIONAL DEVELOPMENT
Rosenbauer invests in its employees by offering customized training and continued professional development programs and helps them to realize their full potential and contribute their skills and expertise to the company.
Training concepts for apprentices
Rosenbauer is heavily committed to training young people and offers apprenticeships in over ten different professions. These range from the traditional office and industry-based management assistant to the metal or mechatronics engineer. Demand for specialists is satisfied in part by apprentices trained in the company. In 2019, a total of 155 young people in Austria, Germany, Slovenia, Italy and Switzerland served an apprenticeship, with around 72.3% studying technical and industrial professions and 27.7% administrative and commercial occupations.
Continued professional development
Rosenbauer continually invests in both professional and personal continuous development, with the aim of preserving and fostering its employees’ qualifications and motivation. In-house and external experts offer tailored training and continuing professional development programs adapted to the working environment. Regular professional development reviews help to determine employees’ needs and development goals. In Austria, Germany and Switzerland, employees have the opportunity to take educational leave or participate in work-based part-time education models.
OCCUPATIONAL HEALTH AND SAFETY
Rosenbauer attaches great importance, both in Production and Administration, to providing employees with a working environment that maintains and ensures their health and well-being. Optimally protecting employees from risks and dangers during their work is a matter of particular importance to us.
Occupational safety
Due to its importance, occupational safety at Rosenbauer is firmly embedded in its organization and procedures: locations in Austria (Leonding Plant I and Plant II, Neidling, Graz, Telfs), Germany (Karlsruhe, Luckenwalde) and Slovenia (Radgona) are certified to ISO 45001. This means that 62% of our employees work at locations with certified occupational safety management systems. The other locations either only became part of the Group recently or are smaller locations for which the effort and expense of introducing a certified management system would be disproportionately high.
In order to optimally protect employees, the company set itself the goal in 2018 of reducing the accident rate to a maximum of 30 accidents per one million working hours by 2023. Various measures are planned in order to achieve this: By 2023, at least three more locations will be certified to ISO 45001 along with each newly opened production location from 2020 onward. In addition, the definition of an occupational accident will be streamlined and the recording of near-miss accidents introduced at all locations.
Focusing on prevention
Many occupational safety measures are aimed at prevention, and thus at reducing the number of accidents. Raising awareness among employees about potential hazards, and identifying and eliminating possible sources of hazards are important measures in this regard carried out at all locations worldwide. Occupational safety is a regular topic at team meetings, and specific occupational health and safety measures are discussed with employees in sustainability workshops. In early 2020, a comprehensive safety campaign took place at all Austrian production locations. The aim here is to boost general employee awareness of occupational safety. In 2019, a prevention campaign on healthy posture and ergonomic movement was held for all employees at the service location in France. The production location in South Dakota (USA) is striving to minimize workplace accidents in cooperation with South Dakota State University.
Occupational accidents | Total | Accidents per 1 million working hours | ||||
---|---|---|---|---|---|---|
2019 | 2018 | 2017 | 2019 | 2018 | 2017 | |
Total | 275 | 221 | 171 | 63,2 | 54.6 | 52.6 |
Austria | 84 | 104 | 68 | 50,7 | 70.0 | 63.4 |
Germany | 167* | 60 | 57 | 235.4* | 83.2 | 71.6 |
Rest of Europe | 8 | 11 | 12 | 31.8 | 48.1 | 59.0 |
USA | 15 | 42 | 34 | 9.4 | 27.9 | 32.2 |
Rest of World | 1 | 4 | 0 | 7.4 | 37.2 | 0 |
* Sharp increase due to stricter recording
Accident statistics
In 2019, Rosenbauer had a total of 275 occupational accidents, of which 106 resulted in more than three days’ sick leave per employee. This results in an accident rate of 63.2 per one million working hours. Accident figures rose sharply year-on-year due to the significantly improved recording of minor accidents at several locations. Accompanied by greater awareness among the employees, this should initially be seen as a success. A permanent reduction of occupational accidents can only be successful once all occupational accidents are recorded with no gaps. As a percentage of all hours worked, those lost due to accidents amounted to 0.3%, equaling the previous year. These occupational accidents were mainly cuts, bruises, lacerations and similar injuries when handling tools and workpieces. There were no fatal accidents in the reporting year. Accidents involving temporary workers are included in the statistics, but not the associated lost hours. In 2020, we will evaluate the reasons for occupational accidents caused by employees of third-party companies at Rosenbauer locations as well as how to record and report them.
Status Goal Occupational accidents
Occupational health
As part of health protection and health promotion, Rosenbauer offers its employees various preventive measures. Across the Group, average sick leave in the reporting year was 9.5 days and thus decreased by one day per employee. In Austria and Germany, employees returning from long-term sick leave are supported by a company reintegration management system used by a majority of the affected employees. This helped six employees in Leonding in 2019, for example.