▸ Products & Society
Products & Society
Rosenbauer offers its customers sustainable firefighting products that combine safety and longevity. In doing so, the company relies on environmentally friendly materials and conserves resources by reducing its consumption of materials, energy and water.
Quality, safety and longevity are the most important aspects for Rosenbauer in the development and manufacture of its products. The company studies social megatrends in detail along with their implications as regards future requirements for emergency services. For example, demographic change and increasing digitalization will have an impact on the way fire services are structured and the technology they use.
One strategic goal is to equip fire services with fascinating, stateof- the-art products. Rosenbauer plays a large part in defining these as it is the firefighting industry’s technology and innovation leader. So for us, research and development are a top priority. The same applies to ongoing product development with regard to environmental impact and ergonomics.
PRODUCTS
Rosenbauer’s main strength is major innovations and pioneering technologies in the production of firefighting vehicles and fire extinguishing systems according to European and US standards. As a full-line supplier, the company provides fire services with firefighting vehicles for municipal use, aerial ladders, hydraulic firefighting and rescue platforms, ARFF vehicles and escape ladders, industrial firefighting vehicles, specialty vehicles, extinguishing systems, firefighting systems, stationary fire extinguishing systems, and telematics solutions for vehicle and deployment management. Rosenbauer provides maintenance, customer service and refurbishment through a service network in over 100 countries.
Status Goal Variety of Training simulators
HEALTH AND SAFETY OF EMERGENCY SERVICES
The health and safety of firefighters is Rosenbauer’s top priority and is always the focus in the use of our products. In addition, product ergonomics and safety devices are being continuously improved. These must provide the fire services with the best possible support and protection as they go about their daily work. Rosenbauer offers comprehensive customer training courses. These range from operator and technical training on vehicles and extinguishing systems, through special tactical training, to simulated deployments.
VEHICLE RELIABILITY AND LONGEVITY
Since firefighting technology has to operate immediately, reliably and flawlessly in the toughest conditions, quality is the primary factor in all products and processes and in Production. The associated reliability and longevity are extremely important, not least because most fire services are publicly funded. In addition to the quality management system, this is guaranteed by Rosenbauer with the use of high-quality materials and components, and continual improvement of product safety and customer service, which ensures safe operation.
Quality
The conditions firefighting technology must be able to withstand are stipulated in strict standards. Rosenbauer meets the highest standards worldwide. The company guarantees quality along the entire value chain with experienced professionals and an ISO-certified quality management system, which is also used to steer and optimize processes and comprises the following standards:
- quality management according to ISO 9001:2015,
- environmental management according to ISO 14001:2015,
- energy management according to ISO 50001:2011, and
- occupational health and safety management according to ISO 45001:2018.
Materials and components used
As a producer of firefighting vehicles, Rosenbauer needs aluminum and steel as primary raw materials. Both metals are easy to recycle but manufacturing them consumes a great deal of energy. Rosenbauer minimizes surface treatments so that the materials can be recycled as far as possible without slags. Other important raw materials come from the plastics industry. Chassis make up the largest share of the Group’s procurement volumes; everything else is materials required in Assembly. Rosenbauer buys almost exclusively prefabricated, mostly ready-to-install parts: for vehicle superstructures these are primarily aluminum sandwich panels, sheets and profiles, for vehicle trims and design fairings, preformed parts made of plastic, the raw materials for which are often pre-colored by the supplier in the vehicle color. Aluminum, stainless steel or gunmetal housing is used for firefighting pumps. The shaft and other pump units are procured as steel blanks and finished in-house.
Number of production locations certified to ISO 9001
Product safety
Ensuring the safety of firefighters in action is a central concern in product development. The stated goal is a steady increase in ergonomics and safety in each product area.
This is why built-in devices to help unload equipment, and on arrival at the scene, the vehicle is lowered. Even the AT (Advanced Technology) – the tried and tested municipal firefighting vehicle from Rosenbauer – is honed to the highest safety standards. All handles and handrails are bright orange. In an emergency, firefighters can see immediately where to grab them or where they can hold on. Doors with stairs lock automatically when leaving the vehicle to minimize the risk of injury and integrated supports provide head protection en route.
Rosenbauer also develops protective clothing for firefighters, manufactured according to customer requirements. The modern suits are not only safe but also lightweight, and their high breathability prevents emergency services personnel from overheating – one of the most common causes of accidents in the firefighting industry.
Customer Service
An important component of vehicle longevity and safe use is customer service. This ensures that Rosenbauer products can be operated safely by users and remain operational throughout their whole lifecycle. The global service organization consists of around 200 service technicians, 25 Rosenbauer service workshops and 150 regional service partners with their own infrastructure.
No vehicle is handed over without prior training. In addition, training4fire offers a comprehensive range of training for fire services, from operator and repair training, to specialist programs for engineers and equipment maintenance personnel, through tactical, operational and driver safety training. Rosenbauer provides a guaranteed supply of spare parts to ensure its products are always ready for operation.
TECHNOLOGY AND INNOVATION
Its focus on technology and innovation enables Rosenbauer to equip fire services with fascinating products. Research and development are therefore core priorities at the company, particularly ongoing product development with regard to environmental impact and ergonomics.
Rosenbauer’s innovation activities have a long-term focus and are based on systematic innovation management. This includes factoring in environmental issues at a very early stage of development through materials analysis, taking account of material workability and recyclability. Rosenbauer continuously and rigorously monitors future issues likely to impact fire services, and uses them to develop innovative product solutions.
Functional design
Rosenbauer products are characterized in particular by functional design and the perfect interplay of the individual components involved. Its position as an innovation and technology leader in the firefighting industry is possible only with an in-depth understanding of future fire service requirements, the expertise of long-serving employees and continuous R&D activity. Equally, customers and users are involved in most of its developments.
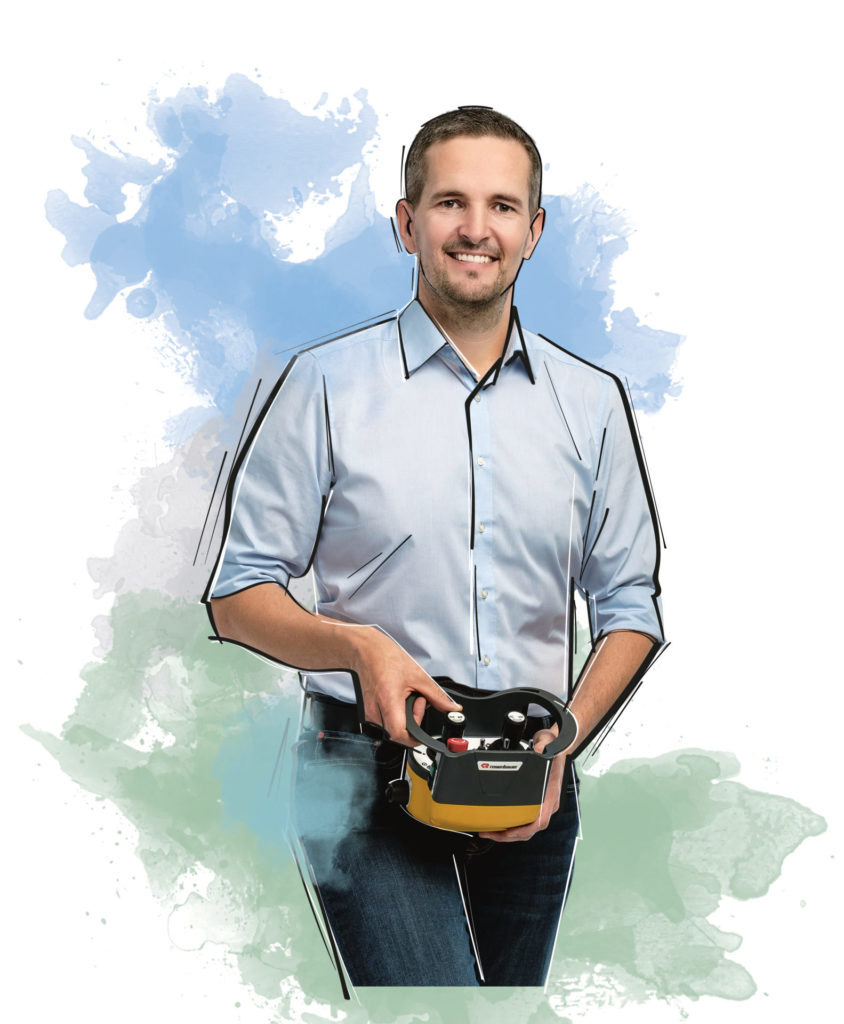
networking
“You could say: We have to put out fires the old-fashioned way. We say: Intelligent networking does the job much better.”
ROLAND WEBER
GLOBAL PRODUCT MANAGER FIRE FIGHTING
COMPONENTS
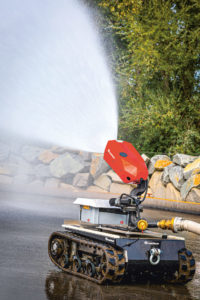
END-TO-END NETWORKING
Digital networking enables fire services to coordinate and monitor their deployments remotely. Robots, drones, augmented-reality systems and digital vital sign monitoring of emergency service workers will improve firefighting outcomes and save lives in the future. We are working intensively on networked products to optimally support fire services with technology during their deployments.
Reducing the environmental impact of products
Furthermore, Rosenbauer takes sustainability into account throughout the entire product lifecycle. For example, environmental impact is considered as early as the design stage, while waste prevention and the efficient use of resources are maximized. This package of measures is designed to provide absolute reliability and longevity in the field.
The superstructures of Rosenbauer firefighting vehicles are largely made of aluminum, as it is significantly lighter and less susceptible to corrosion than steel. AT design allows maximum utilization of the body, higher payloads compared to vehicles with steel superstructures, and superior handling. It also makes the AT municipal flagship easy to recycle at the end of its life.
From 2020, the extinguishing agent tanks in all PANTHER types will be made of PPE (polyphenylene ether) following a final switch. These environmentally friendly tanks are also used across the board in all other vehicle types. In addition, the European PANTHER series is available with a 750 hp Volvo Euro 6 engine. In the United States, this vehicle is available in the best emissions category there – Tier 4 final for non-road engines.
In helmet production, Rosenbauer achieved its goal of conserving 100,000 m² of plastic film in Production each year starting in 2019. This is enabled by the switch to reusable packaging in the production process. Further reductions in disposable packaging will follow beginning in 2020. In addition, most of the helmet shells are now painted by robots. This significantly reduced the so-called overspray, i.e. the part of the applied amount of paint that does not land on the helmet and must therefore be disposed of.
Last year, Rosenbauer invested € 20.2 million in research and development. Its R&D ratio was 3%, and therefore, at the top end of the target range of 2–3% of Group sales.
Product innovations and improvements
Rosenbauer is increasingly focusing on prevention, particularly in its innovation activities. This will prevent damage situations from having to be mitigated in the first place; instead they will be prevented as early as possible. The early spotting of fires and especially forest fires is a key area of emphasis in research in this regard.
A major business goal for Rosenbauer is to manufacture a version of the Concept Fire Truck (CFT) in series production from 2021. The CFT is the innovative concept study of a hybrid firefighting vehicle that caters to fire services’ future needs.
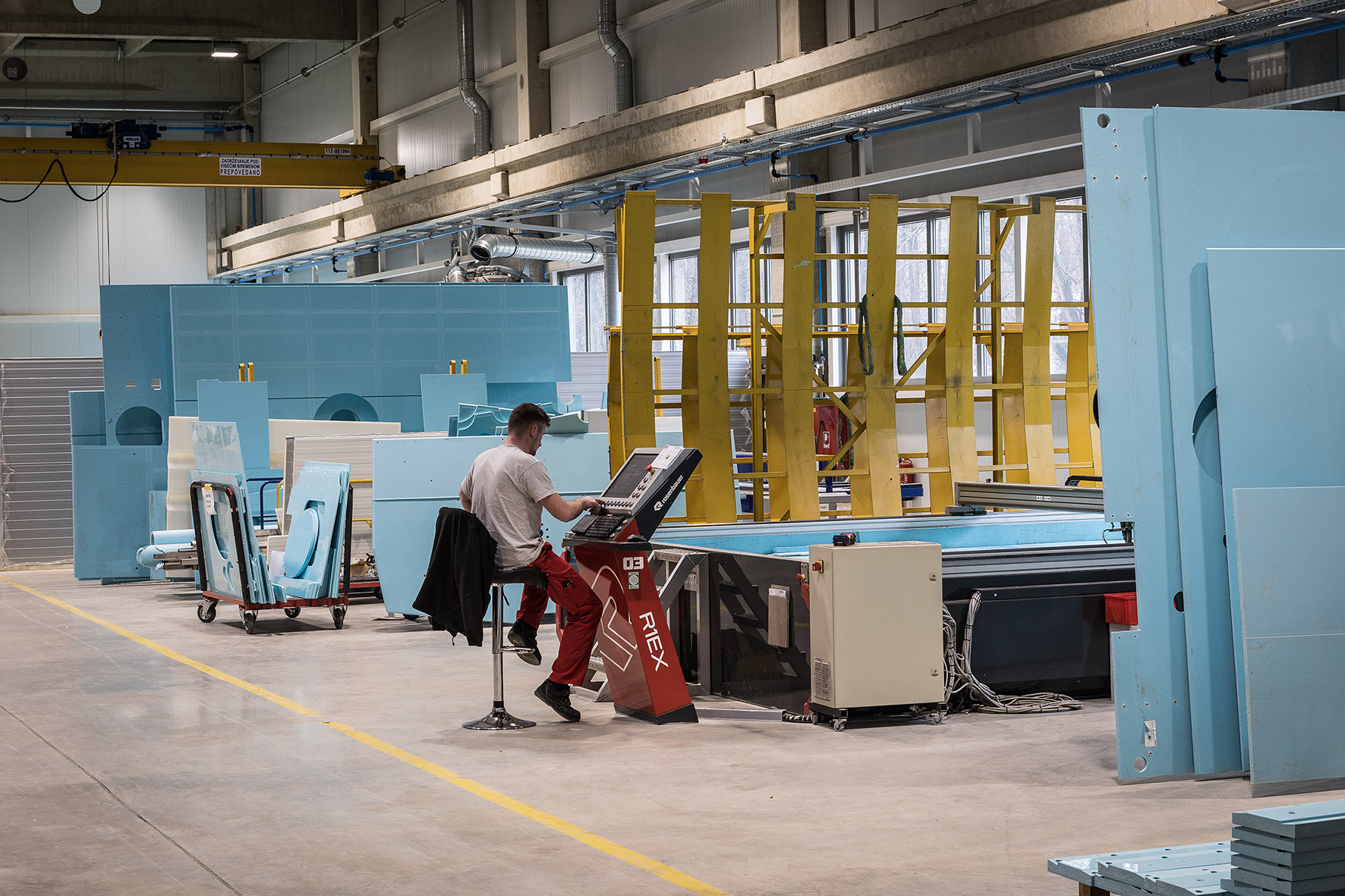
Tank production is largely automated using robots that Rosenbauer has developed itself.
CLOSED-LOOP MATERIAL CYCLE FOR WATER TANKS
Rosenbauer has always taken care to develop products made of environmentally friendly materials. A particularly successful and innovative example is the company’s own extinguishing agent tank production in Radgona, Slovenia. The facility there manufactures tanks from polyphenylene ether (PPE), a material that can be recycled repeatedly.
Extinguishing agent tanks are a feature of almost every firefighting vehicle. The standards for these components are high: They must be as stable as possible, while also being lightweight and resisting corrosion. During deployments, they must be well positioned for turns to enable superior vehicle handling and, of course, not end up as hazardous waste at the end of the product’s life cycle. This is precisely what Rosenbauer has accomplished by manufacturing its own PPE water tanks. Previously, all water tanks were made of steel or glass fiber reinforced plastic (GRP). The latter constitutes a health risk during manufacture and can only be incinerated as hazardous waste. In order to improve the environmental footprint of these products, PPE tanks have been used in most vehicles since 2013. Around 700 units with a capacity of 500 to 18,000 liters are manufactured annually. They are intended for the PANTHER series, all municipal vehicle series and for specialty vehicles. GRP tanks are only used in exceptional cases and upon customer request.
The product itself as well as its production process were developed by Rosenbauer. Since 2015, the light-blue panels have even been welded together by a specially programmed robot after a CNC-controlled milling machine has cut the parts to size. All scrap from Production is returned to the supplier and then simply processed into new panels. If a vehicle with a PPE tank is scrapped, it can be returned to the material cycle, even after a long period of service.