RESPONSIBLE EMPLOYER
Rosenbauer has 4,312 employees worldwide, men and women who make a difference with their diversity and ideas. The company provides an environment in which every employee can contribute their talent and efforts.
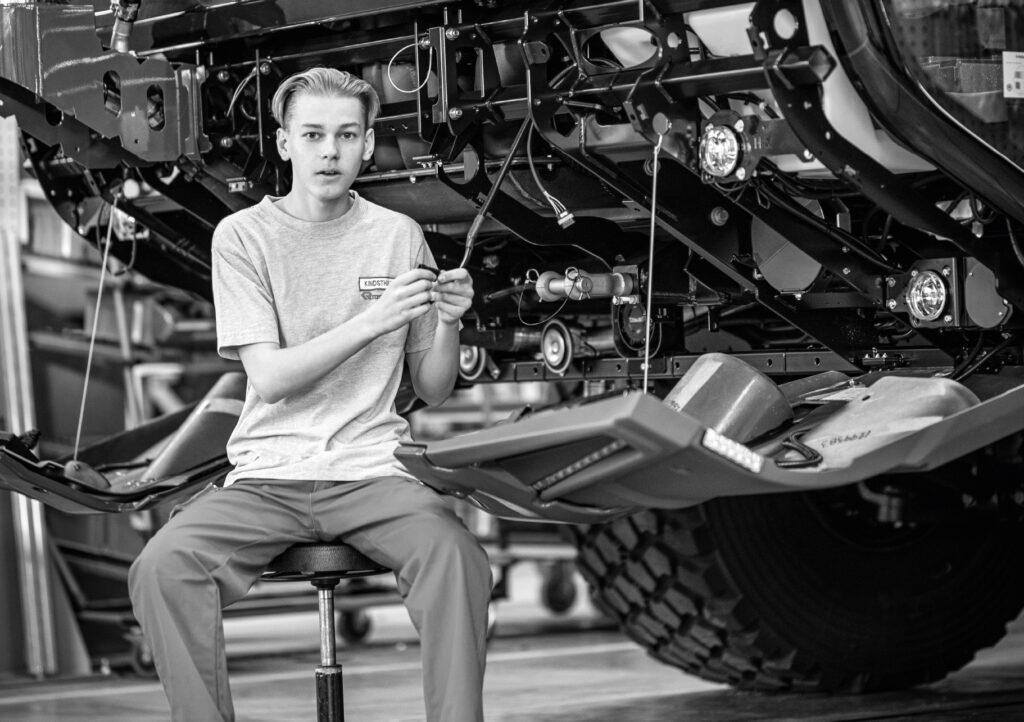
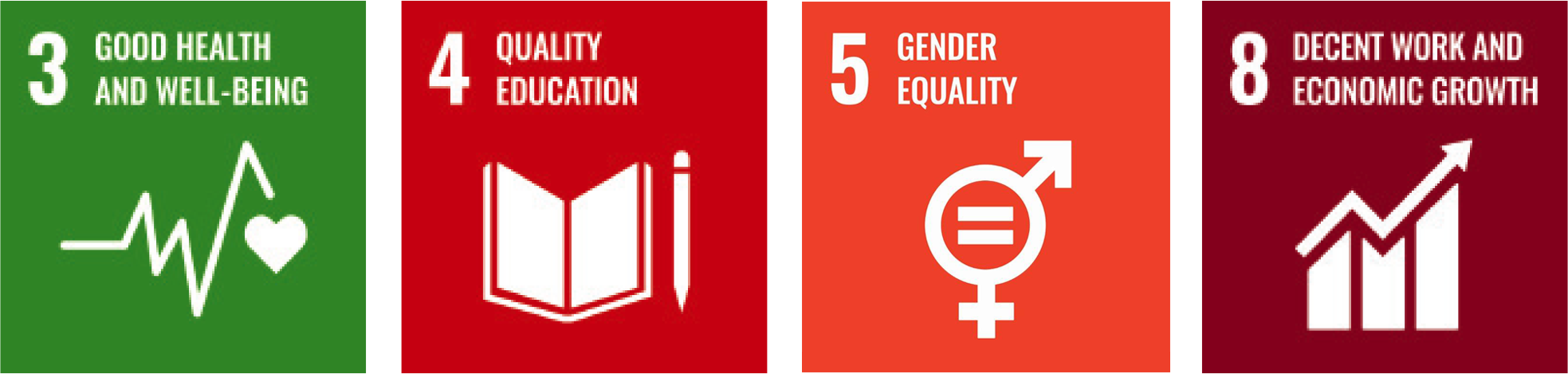
Current social and technical developments are changing the environment in which Rosenbauer and fire services operate. As a result, employees’ needs and requirements are changing. Digital networks and communications have gained in importance.
HR management at Rosenbauer is coordinated globally by the Human Resource Management department at Group headquarters in Leonding (Upper Austria). Larger company locations also have HR departments that cover all local issues. The departments actively exchange information to ensure the provision of training and professional development opportunities. One of HR management’s most important duties is to create a corporate culture and work environment in which employees can evolve and gladly contribute to our mutual success. Global HR management is tasked with monitoring success in the four material areas of activity (training and continued professional development, employee satisfaction, occupational health and safety, and diversity and equal opportunity) and reviewing this using corresponding key performance indicators.
Employment structure
In the 2023 financial year, Rosenbauer had 4,312 employees worldwide – an increase of around 5.7% over the previous year. Of these, 60.3% are blue-collar workers who mainly work in production, assembly and repair, while 39.7% are white-collar workers who work in administration, development and sales. In the Group as a whole, only 6.2% of Rosenbauer’s employees work part time, and more white-collar workers do so (8.6%) than blue-collar workers (4.6%). Rosenbauer supports flexible working hours, and in addition to part-time options also offers flextime models. In the year under review, the flextime agreement was greatly expanded at headquarters, core attendance was abolished, and break regulations were greatly facilitated, especially for part-time employees.
In order to be able to satisfy demand for employees working in production at all times, Rosenbauer also employs temporary workers. They have equal rights to Rosenbauer’s own employees and generally have the opportunity to join its permanent workforce. In the reporting period, the Group had 149 temporary employees (131 in Austria, the others in the rest of Europe). Some 68.1% of all Rosenbauer employees are subject to collective labor agreements.
Employees of Rosenbauer Group by region (headcount) | All employees | Blue-collar workers | White-collar workers | ||||||
---|---|---|---|---|---|---|---|---|---|
2023 | 2022 | 2021 | 2023 | 2022 | 2021 | 2023 | 2022 | 2021 | |
Austria | 1,632 | 1,646 | 1,648 | 875 | 920 | 916 | 757 | 726 | 732 |
Germany | 1,038 | 1,003 | 997 | 733 | 652 | 642 | 305 | 351 | 355 |
Rest of Europe | 413 | 346 | 329 | 222 | 171 | 162 | 191 | 175 | 167 |
USA | 920 | 899 | 985 | 579 | 551 | 619 | 341 | 348 | 366 |
Rest of World | 309 | 184 | 171 | 191 | 91 | 90 | 118 | 93 | 81 |
Part-time rate at Rosenbauer Group (in % and headcount) | 2023 | 2022 | 2021 |
---|---|---|---|
All employees | |||
Total | 268 | 254 | 242 |
Total in % | 6,2% | 6,2% | 5.9% |
Women | 131 | 123 | 126 |
Women in % | 22,2% | 22,3% | 23,1% |
Men | 137 | 131 | 116 |
Men in % | 3,7% | 3,7% | 3,2% |
Turnover
The turnover rate of 13.4% was down by 2.5% on the previous year. This indicates that the general turmoil in the labor market created by the pandemic has somewhat stabilized. Some 17% of the workforce joined the company in 2023 – not including those who were taken on as the result of acquisitions or start-ups that took place in the reporting period.
Suspended or reactivated employment contracts are not included in the KPIs for entries and departures, which is why slight discrepancies may occur in comparison with the total headcount.
STARTING AS A TRAINEE AT ROSENBAUER
Rosenbauer offers graduates with a technical or business background the opportunity to join the Rosenbauer Technical Trainee Program (RTTP). Over an 18-month period, the trainees gain work experience across the various technical departments and at the headquarters in Leonding as well as one other Group location.
Helga Riss and Julia Christina Wolf completed the program in 2023. We interviewed them to find out how they got on and what kind of experience they had.
Helga Riss (left) and Julia Christina Wolf (right) pictured with Sebastian Wolf and Andreas Zeller
Were you always interested in technology? Where does this interest come from?
Helga Riss: My general interest in the technical field was sparked at a very young age on the family farm by taking an active role in the various jobs that had to be done. This inspired me to take mathematical and technical subject options at school. After finishing my technical studies, it was clear to me that I wanted to start my working life at a technical employer.
Julia Christina Wolf: Even as a young child, I had a certain fascination with cars, and at school I was very good at scientific subjects like math, physics and chemistry. After I finished school, I decided to study for a bachelor’s degree in industrial and mechanical engineering followed by a master’s degree in industrial and automotive engineering. In addition, all the internships and student jobs I had were always linked to automotive engineering. So you could say I developed a certain affinity with technology from playing with my Carrera racetrack in my bedroom as a child, and this affinity is still very much alive in my work with firefighting vehicles.
How did you find out about the Rosenbauer program?
Helga Riss: Because I’d already written my master’s thesis at Rosenbauer, I was approached by the HR department and asked whether I would be interested in taking part in the trainee program. I didn’t need long to think about it and said yes right away
Julia Christina Wolf: I found out about the trainee program through an online search. I became aware of Rosenbauer as a company by chance through an episode of “Sendung mit der Maus” that talked about the company and its products.
What were the conditions for taking part in the program?
Helga Riss: As a longstanding member of a volunteer fire service, I was already aware of Rosenbauer. Because of that, I was curious to take a look behind the scenes and learn more about what Rosenbauer was like as a company. I was also interested in doing a trainee program.
Julia Christina Wolf: I think the appealing thing about a trainee program is the chance to gain insight into different areas of a company and different work processes while also having the opportunity to manage projects and build up a network within the company. This allows you to get a better idea of what your strengths in the job are and decide on the specific area you want to work in for the future based on your interests. What is it like as a young woman to work in an environment or business that is traditionally dominated by men?
What were your first impressions?
Helga Riss: Both my male and female colleagues welcomed me with open arms and we worked together as equals right from the start. Due to my affinity with technology, I’d already had previous experience of working in male-dominated fields, so it wasn’t a new experience for me at Rosenbauer. But I want to stress that my experience was an extremely positive one.
Julia Christina Wolf: I was given a very open and warm welcome by everyone and quickly integrated into the teams across the various departments. I was always treated as an equal. Although there were also a few isolated occasions where I was viewed with skepticism as a woman. You’ve got to understand that it’s a bit tense for both sides when there is suddenly a woman sitting in the “man cave.” It’s a situation that takes some time to get used to. It’s not my first time working at a male-dominated company, and I had a very pleasant working relationship with my colleagues.
When you look back and take stock of the last few months, what have you learned?
Helga Riss: At the headquarters in Leonding, I gained considerable experience and expanded my skills working in the various departments. For example, I gained an overall picture of vehicle production in Leonding, Neidling and Minnesota along with an insight into CFD1 simulation (flow analysis), VBA2 programming, project management and process development. The most exciting thing for me was the chance to spend several months getting to know the plant in Minnesota, USA. I got to work on the US launch of the RTX, liaising with customers to fix the equipment assembly schedule, talking them through the development process and giving them a picture of the completion process, and actively supporting them with everyday business.
Julia Christina Wolf: I gained some fascinating insights into various technical areas, and this helped me become much more familiar with Rosenbauer and its structures. Rosenbauer is represented in over 120 countries, and I had the chance to complete a part of the program at the location in Singapore. This gave me the opportunity to immerse myself in a different culture and come into contact with other Rosenbauer products. The trainee program has allowed me to find a technical position that I can see myself doing in the future: work technician on the AT vehicle range. I really like production-related work because of the variety of different tasks and the direct link to the product.
And one final question: Will you continue to work in this field?
Helga Riss: That’s a resounding yes; the interest is there. Following the trainee program, I’ll be working in extinguishing system development.
Julia Christina Wolf: Definitely! The trainee program reinforced my ambition to continue working as an engineer.
Ms. Riss and Ms. Wolf, thank you very much for the interview and the interesting insights.
1 CFD stands for computational fluid dynamics or numerical fluid mechanics
2 VBA stands for Visual Basic for Applications, a programming language
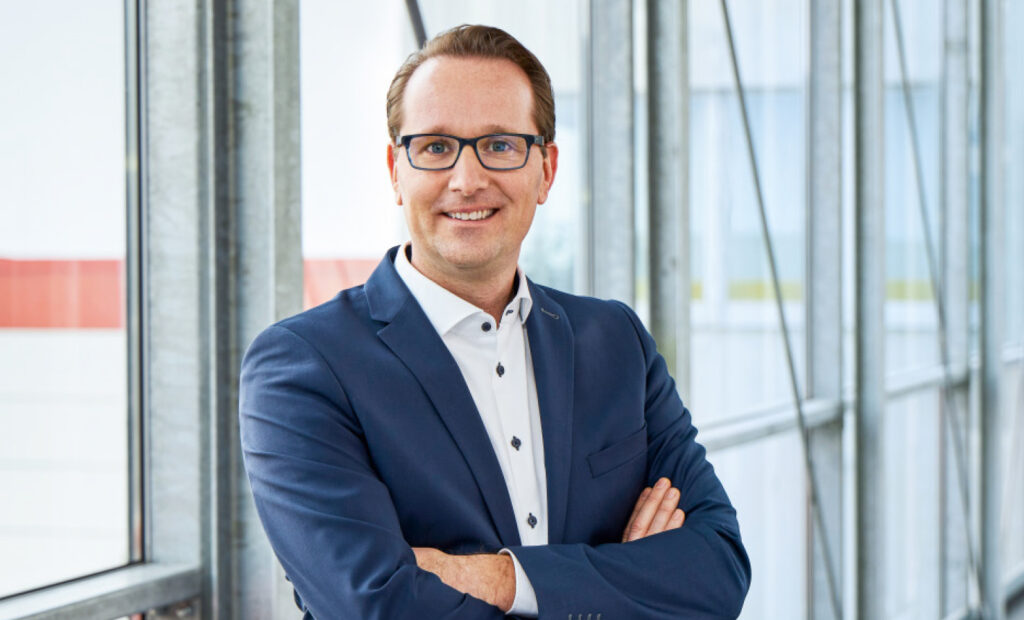
Markus Schachner, Senior Vice President Product Developement, gives us his view on the Rosenbauer trainee program
What advantages do you think the trainee program has to offer?
The trainee program has many advantages because it offers a broad experience that informs trainees about all the possible entry-level positions available at the start of their career before they specialize in a certain professional field. This allows them to develop a broad spectrum of knowledge across the value chain encompassing the whole product portfolio and to build a supportive network that spans the entire Rosenbauer Group. It also gives the company the opportunity to align the different entry-level positions that are available to trainees with their abilities and interests.
Where do you think there is still potential to improve? Compared with Scandinavian countries, Austria still has a very small percentage of women in STEM professions (STEM stands for science, technology, engineering and mathematics). At the same time, experiences across various companies show just how much technical solutions and the efficiency of teams benefit from having women working in technical fields. We need to make a more conscious and targeted effort to get young women engaged with technology and technical pursuits at the various stages when they are developing their interests.
Is it the case that too few women think themselves capable of pursuing this professional route?
I would encourage any woman to embark on a technical career and opt for scientific subject options as early as the school stage. The wide range of career opportunities available, the tailored development prospects in technical professions and, not least, the opportunity to use your own creativity in scientific work tasks should persuade more women to choose this route.
Training and education
Rosenbauer invests in its employees by offering customized training and continued professional development programs and helps them realize their full potential and contribute their skills and expertise to the company. In 2023, the Group spent a total of € 520 thousand (2023: € 580 thousand) on training and continuing professional development. Training courses on specific work-related hazards are held on an ongoing basis.
Measures in this area include:
- a range of digital courses for all larger locations,
- continued professional development programs individually adapted
to the challenges of individual locations, - extensive training of apprentices, and
- the introduction of a standardized record of professional development hours.
Rosenbauer monitors the success of these measures based on the number of continued professional development hours in each employee category.
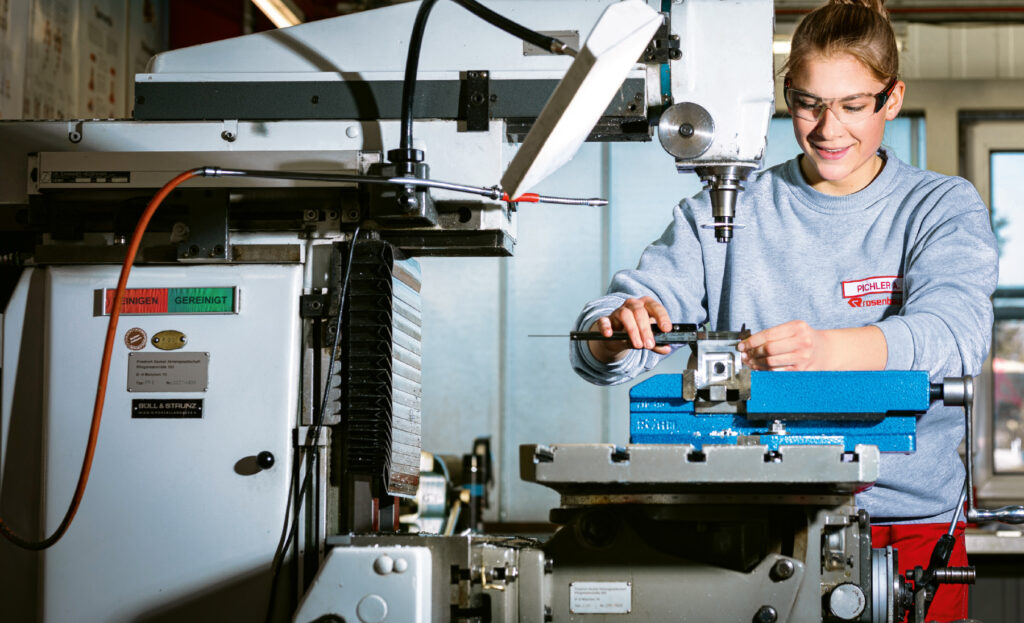
At the training workshop in Leonding, Austria, apprentices are trained in-house.
Training concepts for apprentices
Rosenbauer is heavily committed to training young people and offers apprenticeships in over ten different professions. These range from industry-based management assistant to metal or mechatronics engineer. Demand for specialists is satisfied in part by apprentices trained in the company. Young people are familiarized with numerous areas of responsibility and departments during their apprenticeships.
Apprentices are taught manual skills and prepared for a job in Production by experienced instructors in a dedicated teaching workshop in Leonding and at specialized schools in other locations. Training is also available in diverse subjects such as business etiquette, social skills and handling money, in order to teach young people skills that will benefit them outside the workplace, too. Sustainability issues are integrated into the training apprentices receive.
In 2023, a total of 164 young people in Austria, Germany, Switzerland and Italy served an apprenticeship with Rosenbauer, with around 76% studying technical and industrial professions and 24% administrative and commercial occupations.
The two largest US locations in Wyoming (Minnesota) operate a separate training program for young employees. This provides the opportunity to receive technical training since apprenticeships are not common in the United States.
Rosenbauer also trains young people with special needs in cooperation with charitable organizations. The aim here is to integrate them into the workplace and the social structure to the greatest possible extent.
Number of apprentices at Rosenbauer 2023
Continued professional development
Rosenbauer continually invests in both professional and personal development, with the aim of preserving and fostering its employees’ qualifications and motivation. In-house and external experts offer tailored training and continued professional development programs adapted to the working environment. At the Austrian, German, and Swiss locations, courses can be booked on the company portal, which will be rolled out to other locations. Regular professional development reviews help determine employees’ needs and development goals. In the reporting year, each employee had an average of 6.3 hours of traditional continued professional development, with white-collar workers spending approximately 11.1 hours in training and blue-collar workers 3.1 hours. However, these statistics do not take account of learning on the job, which is typical in the area of Production. Not all locations record statistics on continued professional development hours.
Employee satisfaction
Employee satisfaction is the result of many issues that intersect and interact. Rosenbauer regularly conducts annual development reviews and uses these as a basis for determining actions to take to motivate employees for the long term. These measures are intended to address the requirements of Rosenbauer as an employer, while also meeting the needs of blue-collar and white-collar workers. These include
- targeted career planning,
- binding employment contracts, and
- benefits above and beyond regular salary.
Rosenbauer is perceived as an attractive employer, which is underscored, for example, by its employees’ long periods of service with Rosenbauer. The success of these measures is monitored according to the annual turnover rate.
Period of service
A long period of service with the company underscores a high degree of employee satisfaction and identification with Rosenbauer. More than 35.5% of employees at the locations in Austria have worked at Rosenbauer for more than ten years, of which 14.1% have been with the company for more than 20 years. In Switzerland, 20% of the employees have worked at the company for over ten years, while in Slovenia it is 23%.
Evaluation of mental stress in the workplace
In Austria, we are legally obligated to evaluate sources of stress in the workplace. This effort began in 2014 at Rosenbauer and was completed at all locations in Austria as part of a multi-stage process. Information about workplaces not fitting into this category and smaller units was collected in group and individual interviews. The monitoring process began in 2021. The effectiveness of the agreed measures was discussed, potential new measures were set out, and the process of implementation was started.
Performance reviews for employees at all levels
Regular performance reviews are part of responsible corporate culture at Rosenbauer and are conducted in the spirit of open and respectful dialog. Based on a discussion guide, these are held regularly between employees and their direct supervisors on a mandatory basis. In the course of these meetings, the past year, performance, skills and qualifications are discussed with employees along with professional development opportunities. Future work priorities, target agreements, and development and training measures are also agreed. These discussions with employees were held at all levels at Rosenbauer again in 2023.
Family support program for parental leave
As a responsible employer, Rosenbauer aspires to offer its employees an optimal work-life balance. This includes improving the compatibility of work and family life. Since 2015, Rosenbauer has operated an in-house daycare center for employees’ children adjacent to the Group’s headquarters in Leonding. For older children, Rosenbauer offers a summer camp during school holidays that is financially supported by the company. Rosenbauer supports flexible working hours and offers both part-time and flextime work, or work-from-home days.
In Europe a dedicated familiy program allows men to also take parental leave. At the headquaters in Leonding 14 men took this opportunity in the year under review.
Occupational safety has top priority in the production of vehicles.
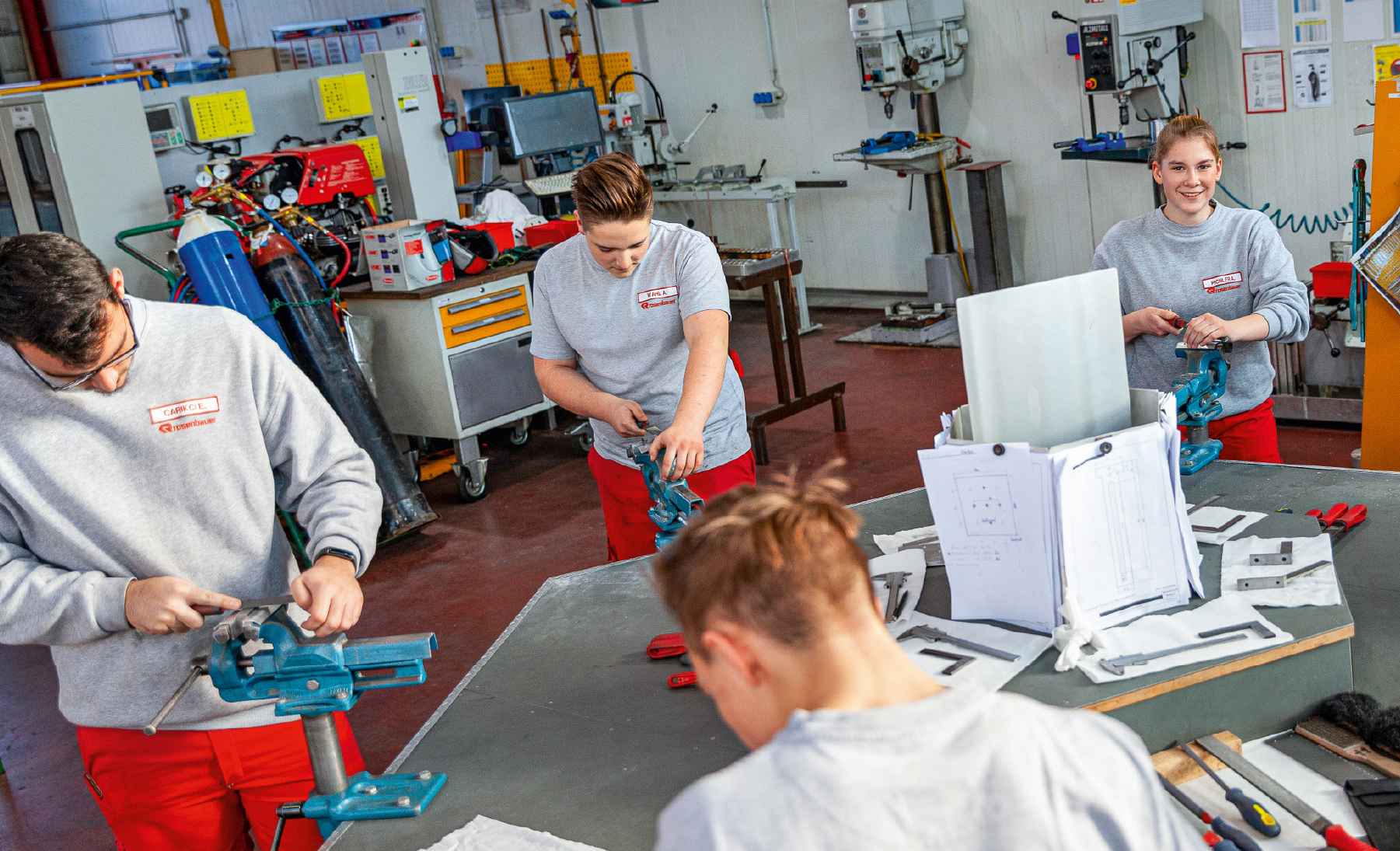
Occupational health and safety
Rosenbauer attaches great importance, both in Production and Administration, to providing employees with a working environment that maintains and ensures their health and well-being. Optimally protecting employees from risks and dangers during their work is a matter of particular importance to us. In this context, Rosenbauer takes the following measures:
- Preventive measures to avoid mental stress
- Safety campaigns
- Providing protective work clothing and personal protective equipment
- Mandatory safety briefings
- Increased bonus for safety tips and ideas to prevent accidents
- ISO 45001 certification
Rosenbauer is taking additional steps to promote employee health with management of reintegration into the company and the “Enable me 50+” project to provide support for employees returning from long illnesses, for example in adapting their workstations.
Key indicators in this area are the number of occupational accidents, the number of lost working days, and of sick days per employee.
Prevention at the fore
Many occupational safety measures are aimed at prevention, and thus at reducing the number of accidents. Raising awareness among employees about potential hazards, and identifying and eliminating possible sources of hazards are important measures in this regard carried out at all locations worldwide. There is a risk of injuries with serious consequences when work is carried out on vehicle roofs, when vehicles are driven on public roads, and during maneuvering in the production halls. The issue of occupational safety is regularly discussed in team meetings.
Accident statistics
In 2023, a total of 251 occupational accidents occurred at Rosenbauer, of which none had serious consequences, while 85 occupational accidents resulted in more than three days’ sick leave per employee. The company set itself the goal in 2018 of reducing the accident rate to a maximum of 30 accidents per one million working hours by 2023. At 42.0 accidents per one million working hours, the accident rate is on the same level in the year under review compared with the previous year. In line with the GRI index, since 2021 the working hours of all employees have been counted and no longer only those in the so-called productive work areas.
As a percentage of all hours worked, those lost due to accidents amounted to 0.1%, which also represents a fall compared with the previous year. However, this is due to the fact that since the 2021 reporting year, the working hours of all employees have now been counted. Previously, only hours worked in Production were reported. These occupational accidents were mainly cuts, bruises, lacerations and similar injuries when handling tools and workpieces. There were no fatal accidents or occupational accidents with serious consequences in the reporting year. Accidents involving temporary workers are included in the statistics and are also reported.
Status goal: Workplace accidents per 1 million working hours
In 2022, 24 ideas for improving occupational safety were submitted in Austria alone. Employees are informed and made aware before starting their activities – and at regular intervals thereafter – by workplace inspections, and instruction and training on safety risks and potential hazards. In 2023, 44 near-miss accidents were reported across the Group which is due to the improved documentation since 2021.
In addition, wherever production areas are reorganized and modernized, Rosenbauer considers short routes, optimal equipment support, ergonomic access to materials, mobile tool trays and energy sources.
If occupational accidents do occur despite all precautions, they are recorded in a reporting system based on standardized specifications. The internal indicators are hours lost as a result of occupational accidents, the number of accidents itself and sick leave. Occupational accidents are reviewed with the relevant executive and safety representative. Building on this, we develop measures ranging from training to changes in workflows to prevent this type of accident in the future.
Occupational accidents at Rosenbauer Group | 2023 | 2022 | 2021 |
---|---|---|---|
Work-related injuries | |||
Employees and workers | |||
Number | 251 | 266 | 265 |
Occupational accidents per 1 million working hours | 42.0 | 45.7 | 43.7 |
Leasing staff | |||
Number | 29 | 15 | 15 |
Occupational accidents per 1 million working hours | 59.3 | 65,7 | 62.5 |
High-consequence work-related injuries | |||
Employees and workers | |||
Number | 0 | 0 | 0 |
Occupational accidents per 1 million working hours | 0 | 0 | 0 |
Leasing staff | |||
Number | 0 | 0 | 0 |
Occupational accidents per 1 million working hours | 0 | 0 | 0 |
Occupational health
As part of health protection and health promotion, Rosenbauer offers its employees various preventive measures. In Austria, an in-house sports association helps the workforce stay fit and covers the costs of taking part in sports events. Health programs at various locations motivate employees to choose a healthy lifestyle. The occupational physicians, psychologists, and physiotherapists play a central role in Rosenbauer’s occupational medicine efforts.
Throughout the Group, the average number of sick days per employee in the reporting year stands at 12.4 days, which equates to an increase of 0.9 days compared with the previous year. In Austria and Germany, employees returning from long-term sick leave are supported by a company reintegration management system taken advantage of by a majority of the affected employees. This helped 17 employees in Austria in 2023, for example.
Rosenbauer’s occupational safety organization generally consists of the occupational health service, safety specialists, safety confidants, first aiders, fire protection officers, and employee representatives. Safety teams are in place at all production sites.
The US locations offer a “Frequent Fitness Program” aimed at promoting health. In addition, Rosenbauer offers healthy meals and quit-smoking programs. A comprehensive fitness program for the workforce is also offered in Slovenia. This covers topics such as exercise, nutrition, tobacco and drug use, and general occupational safety issues.
No hazardous substances in Production
Due to the overwhelming amount of assembly work, none of Rosenbauer’s occupational activities represent a serious health risk. Increased safety requirements exist only at those production facilities where parts are glued or painted. Naturally, all statutory regulations are complied with at these locations. Moreover, Rosenbauer has used paints free of heavy metals since 2018.
Diversity and Opportunities
Rosenbauer believes that a respectful and open corporate culture promotes and advances diversity. It is therefore committed to a work environment that is free from prejudice and discrimination of any kind. Employees are treated with the same respect and tolerance regardless of their gender, age, sexual orientation and identity, nationality, ethnic origin, religion and ideology. In order to make this absolutely clear to the wider world as well, the company signed the “Diversity Charter” in 2017.
The topic of diversity also includes fair remuneration, where the focus is on the competence brought to the table. Rosenbauer pursues a salary policy that provides for equal pay for equal performance, considering market conditions. The level of remuneration paid to employees is based on the knowledge they contribute, the work tasks assigned, and the requirements on local markets, and does not differentiate according to gender, origin, or other personal characteristics.
In the interest of increasing diversity and equal opportunity, Rosenbauer targets the following measures:
- Introduction of a technician trainee program
- Implementation of employer branding measures
- Strengthening of female recruiting
- Group-wide establishment of the women@rosenbauer initiative.
Rosenbauer resolutely opposes any form of discrimination. Unequal treatment or discrimination can be reported to the Compliance Officer at any time. In the reporting period, one allegation of discrimination became known in Germany. Rosenbauer is endeavoring to clarify this allegation in a targeted and rapid manner.
People with disabilities make up 4.1% of the workforce worldwide. Rosenbauer works with social psychologists on their employment. What is more, several locations work with sheltered workshops.
For example, the location of Rosenbauer Italia, which has decided to enter into profitable cooperation. The external cleaning service of the service location there is run by the social cooperative SIAA (Servizi Integrazione Alto Adige). The cooperative mainly employs people who would have no chance in the local labor market. In the case of the cleaning service, it is young people with mental illnesses or who have overcome addictions. They are treated by a dedicated psychologist and have close contact with the Rosenbauer employees. At the employees’ request, the cleaning personnel even received the same Christmas present: “They should feel that for us, they belong here,” said the workshop manager Paul Horrer. The quality of the cleaning service is outstanding and the collaboration with the cooperation is going so well for all those involved that it is even being expanded. Thus the catering service of SIAA has already been engaged and the cleaning service is also to be expanded to cover certain production areas.
Status Goal Proportion of Women: achieved
Equal opportunities: women@rosenbauer
Rosenbauer strives to give every employee the same opportunities – regardless of origin, age, gender, culture, or background. To promote diversity, Rosenbauer founded the women@rosenbauer initiative in 2021 and further broadened it in Austria in the year under review. New projects were defined and implemented in nine working groups and with the involvement of female Rosenbauer employees. In addition to training courses for employees – particularly apprentices – on respectful interaction with one another and on the whistleblower system, a new guide for expectant mothers and fathers was also created. This summarizes the most important information in a compact form, from pregnancy to birth to returning to work.
Women@rosenbauer is primarily aimed at networking among female employees and providing mutual support. Initiatives such as the expansion of company sports activities for female employees, internal events, or participation in external activities offer an ideal starting point for exchanging ideas with Rosenbauer employees or with women from other companies.
According to a study by McKinsey*, only 22% of tech jobs in Europe are currently held by women. This is also reflected in the Rosenbauer Group, with a professional environment traditionally dominated by men. For this reason, another focus is on recruiting, which explicitly aims to attract more women to Rosenbauer in the future, especially in technical professions. Several measures are being supported to get girls interested in technology as early as school age. In September 2022, a firefighting training course for girls aged 8 to 12 was held at the Leonding location. As part of the “International Summer Academy in Engineering for Women” at the University of Applied Sciences Upper Austria, 23 female participants from 13 different countries visited the Rosenbauer location in Leonding to learn about the development and production of firefighting vehicles.
In the recruitment process, care is taken to treat male and female applicants equally. The total percentage of women in the Group is 13.7% and is therefore 0.2% higher than the previous year. The initial focus is always on increasing the proportion of women in general, but especially in management at Rosenbauer International. Corresponding measures are being developed by HR together with the women’s network and implemented step by step.
With the launch of the women’s initiative, the targets for the proportion of women were also brought into focus. The target set for the first time of employing 540 women in the company by 2023 was achieved in 2021. Rosenbauer now aims to achieve a 15% share of women by 2025, both in the overall workforce and in the top two levels of management. Employees with responsibility for staff at the individual locations were used for the calculation. As a manufacturer that takes on apprentices, Rosenbauer’s stated objective is to encourage girls to follow a technical career path. The percentage of young women doing an apprenticeship was 24.0% in 2023. Female apprentices in Production accounted for a share of 12.6%. The target of increasing the proportion of female industrial apprentices to 10% by 2023 was therefore already achieved in 2021.
Status Goal Proportion of Women: achieved per 2023: 13,7% Goal by 2025: 15% Proportion of Women The initiative will be continued in 2023 with the full support of the Executive Board and is intended to promote women at all levels in the Group. Performance-related pay and raising employee awareness through gender-neutral language are a matter of course. To raise the measures initiated (soft facts) to a reliable level (hard facts), Rosenbauer plans to develop a set of indicators for gender equality together with Human Resources and the sustainability officers and to include them in sustainability reporting. Integration into the IT system already in use for recording the indicators is planned, depending on the degree of freedom of the system.